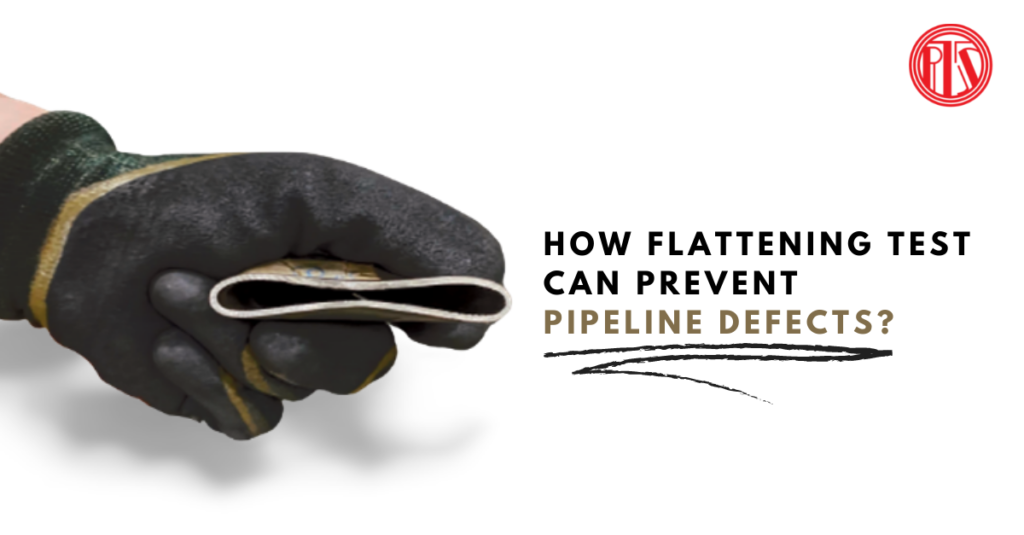
What is flattening test?
Our flattening test on metal sample
ISO 8492 international standards specify flattening tests to determine the ability of metallic tubes of a circular cross-sectional area to undergo plastic deformation by flattening. It is used to reveal the defects in the pipes.
The principle is to apply the length of the steel tube to the specified length of the sample or seamless steel pipe end. By calculating the distance between the two pressing plates under the action of force, we can apply visual inspection to estimate the value stipulated in the relevant product standards.
History of seamless steel pipes & welded pipes
Image via link
Each year, millions of tons of steel pipe are produced. Its versatility makes it the most often used product produced by the steel industry. Steel pipes are found in a variety of places. Since they are strong, they are used underground for transporting water and gas throughout cities and towns. They are also employed in construction to protect electrical wires.
In 1815, William Murdock invented a coal-burning lamp system. To fit the entire city of London with these lights, Murdock joined together the barrels from discarded muskets. He used this continuous pipeline to transport the coal gas and kick start the welded steel pipe industry.
In 1885, the German Manmesmann brothers invented the process of producing seamless steel tubes directly from the bar 1885. By 1895, the first plant to produce seamless tubes was built. As bicycle manufacturing gave way to auto manufacturing, seamless tubes were still needed for gasoline and oil lines. This demand was made even more significant as larger oil deposits were found.
What the type of pipeline defect and how you can prevent them?
Image via link
In 1980, the semi-submersible platform Alexander Kielland suddenly capsized during a storm in the North Sea. One of its five vertical columns supporting the platform was broken off due to a fatigue crack, which had propagated from the double fillet weld near the hydrophone.
Nowadays, when a new pipeline is being installed, operators are focused on ensuring the pipe is safe, reliable and productive. They must adhere to strict standards set by several organizations and want to install pipes with first-class integrity and no defects.
- Corrosion risk
The corrosion process causes metal loss, reduction in pipe wall thickness and loss of strength, leading to pinholes, cracks and splits. Corrosion is a time-critical issue – and failing to tackle it quickly can cause leakage and even rupture of the pipe – resulting in lower production, environmental damage and reduced income.
- Stress corrosion cracking
The combination of a corrosive environment and high pressure causes stress corrosion cracking (SCC), a risk for buried or subsea pipelines. Clusters of small cracks appear on the pipe’s surface; if left untreated, the clusters can start to link together. This forms longer and deeper cracks which can eventually result in pipeline failure. SCC also creates weak points along a pipe that make it more vulnerable to third-party damage or overpressure incidents.
- Weld defects
During welding, defects can occur for several reasons, such as poor welding technique, substandard materials and physical attributes such as dents caused by the manufacturing process or poorly matched pipes. Weld defects can cause pinholes, cracks, incomplete welds, porosity and other problems that lead to weak spots or corrosion sites within the pipe. These defects are often not spotted until late, when the weld has passed through several processes, possibly even aboard a pipe lay vessel at sea, causing delay and high cost.
Our mechanical testing and inspection of your seamless steel tube sample
In order to verify the mechanical properties of seamless steel pipe, our testing specialist will work with you to ensure that the test sample of seamless steel pipe mechanical performance is prepared carefully.
Our testing team will test your pipe samples based on project needs. Mechanical property tests include tensile strength, yield strength, elongation, impact energy, flattening, flaring, etc.