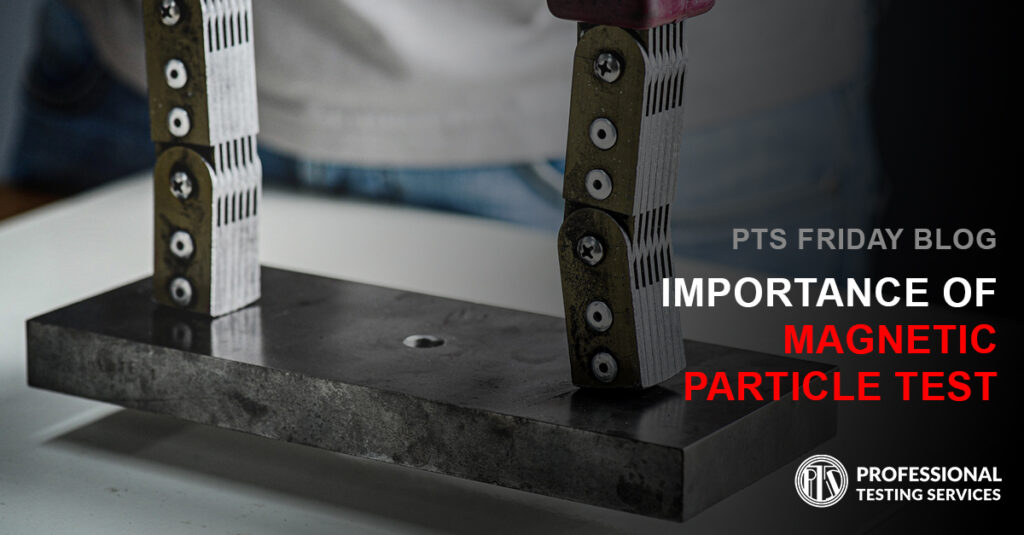
1) MAGNETIC PARTICLE TESTING WAS INITIALLY USED TO TEST FOR DEFECTS IN CANNON BARRELS
In 1868, Saxby reported that magnetizing defects in cannon barrels and other iron components could be detected if magnetized by passing a magnetic compass over them. No particles were used, but the principle of seeking leakage fields was used.
It was in the I920s that the use of magnetic particles for detection and other magnetic discontinuities in magnetized iron and steel was recognized.
2) ONLY METALS CAN BE USED IN MAGNETIC PARTICLE TESTING
MPI Testing can only work on materials that can be magnetized, which are called ferromagnetic materials. Some examples of ferromagnetic materials include steel, cobalt, iron, and nickel.
Aluminum is used for an estimated 80% of aircraft materials today because it is lightweight, robust, predictable and inexpensive. It is also one of the most common metals tested with magnetic particle inspection that cannot be magnetized.
3) DISCONTINUITIES ARE HARDER TO DETECT WITH THE SURFACE COATING
Conduction coatings can mask discontinuities, and it must be demonstrated that unacceptable discontinuities can be detected through the layer. If there is a thick coat of paint or a protective coating, it will cause issues with MPI.
While the metal substrate will still be magnetic, the outer coat won’t be. As a result, it may not allow a tester to see where there are discontinuities in the item. The main principle of MPT is the magnetization of the specimen for producing flux or magnetic lines in it. If the flux lines encounter a discontinuity (like a crack), they create secondary magnetic poles at their faces.
4) ADDING PARTICLES WILL MAKE IT EASIER TO DETECT INDICATIONS OF DEFECTS
The inspection process begins with the magnetization of the component. After the component has been magnetized, iron particles are applied to the surface of the magnetized part. The surface is then coated with small magnetic particles, usually a dry or wet suspension of iron filings. Surface cracks or corrosion pits create a flux leakage field in the magnetized component.
The particles will be attracted and cluster at the flux leakage fields, thus forming a visible indication that the inspector can detect. This enables the detection of defects oriented in any direction in one operation.
5) NOT ALL MATERIALS MAGNETIZE THE SAME WAY
Magnetic permeability is the characteristic of a material representing the establishment of an induced internal magnetic field by an external magnetic field. Magnetic permeability is the proportionality between the induced area and the applied magnetic field strength.
As varied materials have different permeability and retentivity, some parts may look the same, but they are made of another material. Therefore, using the same testing methods may not be applicable. Permeability affects how easily magnetic current travels through the part and gets attracted to small flux leakages because of flaws. A material’s retentivity affects how well it holds its magnetic field.
CONTACT US FOR YOUR MPI TESTING NEED
In PTS, our certified MPI testing team has years of experience performing magnetic particle inspection, and we offer world-class magnetic particle testing examinations to ensure the quality of your sample is compliant with national and international standards.
Talk to us today to find out more.