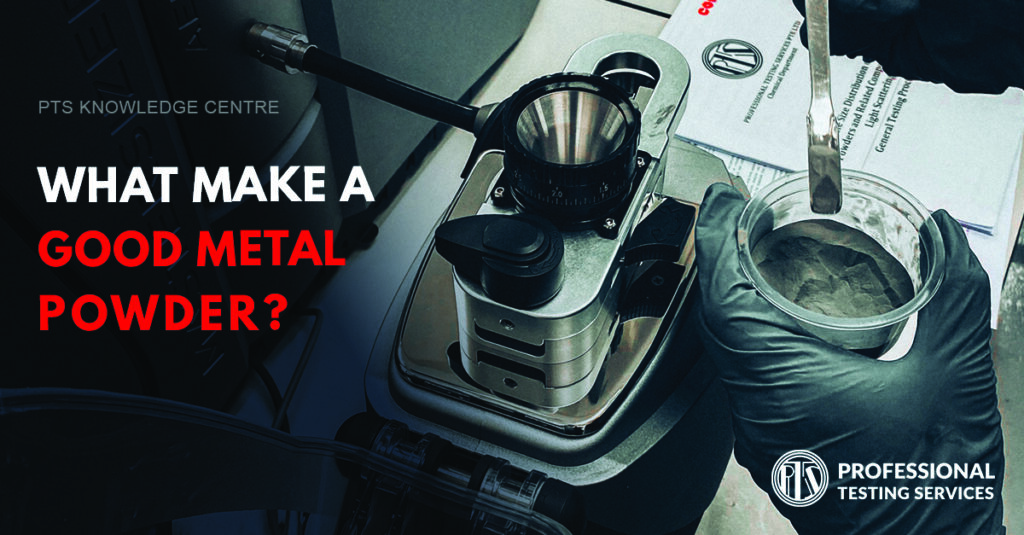
How Metal Powder Make An Impact On Additive Manufacturing (AM)?
Metal powders have been used in a wide range of industrial applications for over a hundred years. They are used from food packaging to super alloy gas turbine discs.
By using metal powders, additive manufacturing allowed several production steps to be merged into one. This enabled mass customization for metal parts. Currently, most of the additive manufacturing machines does not offer any form of responsive control. The printing processes are operated with fixed parameters for a specific application. Thus, inconsistent input material properties will lead to inconsistent finished component properties.
With poor powder quality, it can produce defects in the end part such as pores, cracks, inclusions, residual stresses and suboptimal surface roughness, as well as compromising throughput.
What Makes A Good Metal Powder?
- Chemistry
A powder needs to comply with the alloy composition of the material specified. Grade must be carefully selected so as to control the interstitial elements present such as oxygen or nitrogen. This can impact the properties of the finished part.
In addition, the metal powder must be free from foreign particulate contamination, such as from other material batches at the powder production plant or the AM facility. Contaminant levels of just a few parts per million can be significant in terms of component quality
- Packing Density
Metal powders with a high and constant packing density provide superior production properties with fewer flaws and consistent quality, which can protects itself from compression and impact during storage and transport.
Non-spherical particles give a lower random packing density than spherical particles.
- Flowability
Flowability is closely associated with process efficiency. The ability for metal powders to spread evenly and smoothly across a bed, and to form a uniform layer with no air voids is essential for powder-bed fusion processes.
Smooth, regular-shaped particles flow more easily than those with a rough surface and irregular shape. Rougher surface will lead to an increase interparticular friction. Irregularly shaped particles are more prone to mechanical interlocking. Both powder types decrease flowability.
- Size
Particle size distribution is critical attributes for process control. As well as having a direct impact on powder flowability, size also influences the ability to deliver a uniform, powder bed density. This will determine the energy input needed to bind particles. At the same time, it will affect the surface finish of the built part. Similarly, spherical particles tend to pack more efficiently than those that are irregular giving rise to higher bulk densities.
However, finer powder can be problematic in terms of flowability. The forces of attraction between finer particles increase with decreasing particle size. Finer powders are usually less free-flowing than coarser analogues. However, optimizing particle shape can help to mitigate this effect.
- Internal Porosity
Internal porosity can indicate the final mechanical strength of the finished component. Porosity is usually controlled to minimize its effect on material properties, hardness, and surface finish. However, porosity can actually be a designed parameter for the final product.
Mercury intrusion is a proven technique for quantifying porosity characteristics of powders and formed product. This technique utilizes mercury to probe the surface accessible pores of powder material.
Besides speed, accuracy, and a wide measurement range, mercury porosimetry is able to assess pore size distribution, total pore volume, total pore surface area, median pore diameter, bulk and skeletal density, and percentage porosity.
Professional Testing Services Tests Your Metal Powders
Professional Testing Services analyses your metal powders for the correct chemistry, particle size distribution, and physical and mechanical properties to determine if the powder is ready for 3D printing.
Our team of testing specialist provides a comprehensive metal powder analysis to fully characterize the metal powders used in Additive Manufacturing.
Professional Testing Services – List of Metal Powder Testing
Properties | Method | Test Method |
Elemental Composition | ICP-OES | Alloy Dependent |
Interstitial Gases (O,N,H) | Inert Gas Fusion | Alloy Dependent |
Interstitial Elements (C, S) | Combustion | Alloy Dependent |
Element Mapping | SEM-EDX | For Info only |
Particle Size Distribution | Laser Diffraction | ASTM B822 |
Moisture Analysis | Karl-Fischer Titration | For Info only |
Apparent Density | Hall Funnel (Free Flowing) | ASTM B212 |
Flowability | Hall Flowmeter | ASTM B213 |